Replacing and Fitting Fire-Safe Materials
Removing combustible materials and replacing them with modern, fire-safe equivalents in residential blocks
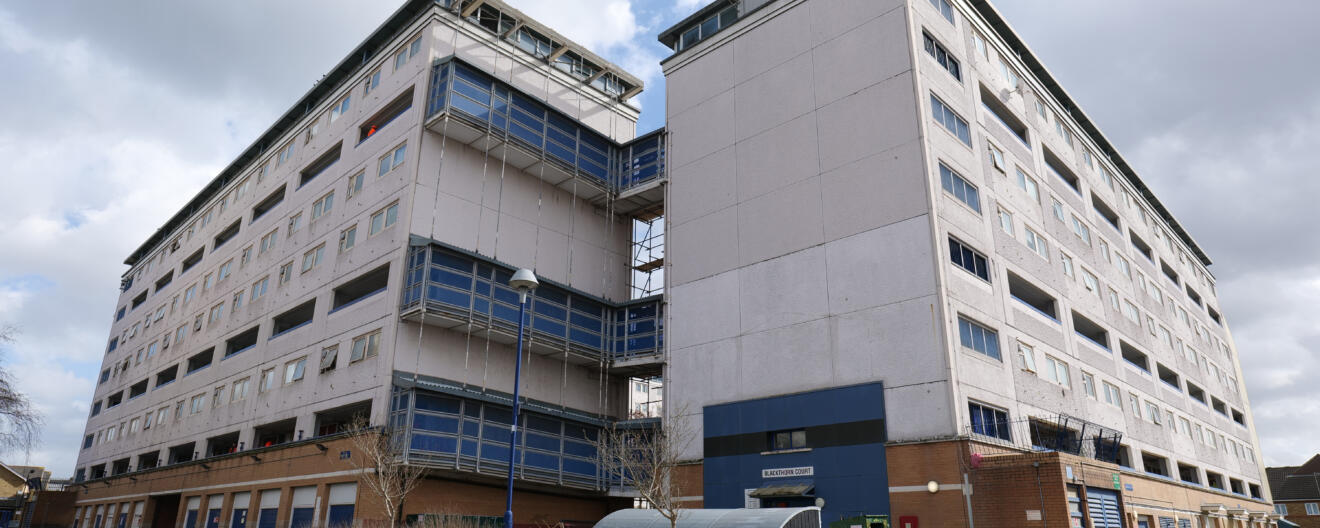
- Stripping out high pressure laminate ceiling panels
- Removing existing extruded polystyrene insulation and associated fixings in communal walkways, balconies and lobbies leading to stairwells
- Installing Hardie panels and thermal insulation (Euroclass A1 or A2-s1 standard)
- Safely disposing of removed materials with responsible companies
- Fitting fire boarding around existing door surrounds
- Removing combustible materials above garage doors and replacing with modern, fire-resistant boarding
- Maintaining clear documentation for the Golden Thread
After the Grenfell disaster, councils across the country began carrying out urgent surveys of their high-rise properties to check for potentially combustible materials.
In Waltham Forest, building safety has always been a priority for the local council, which subsequently set aside an additional £40 million for safety improvements. After carrying out extensive surveys, high-rise residential properties that were identified as containing potentially combustible materials were flagged for remedial work.
These properties included Gean Court, Rosewood Court, Mulberry Court A & C and Blackthorn Court on Avenue Road in Leytonstone.
Because of the materials they contained, a waking watch was established to reassure residents and ensure the building’s safety. Despite being marked for future demolition, the Council decided to upgrade these blocks’ fire safety materials in the interim to cut the risk of fire, keep residents safe and disband the waking watch.
To carry out this work, they called upon our experienced teams, who would need to remove, replace and dispose of the old panelling and fittings.
Our team would also need to provide records and documentation of the work in order to sustain the ‘Golden Thread’ of building safety information, an initiative that was implemented in the Building Safety Act 2022. By maintaining the Golden Thread, responsible people can ensure (and prove) that the building meets safety regulations and identify, remove or mitigate any risks.
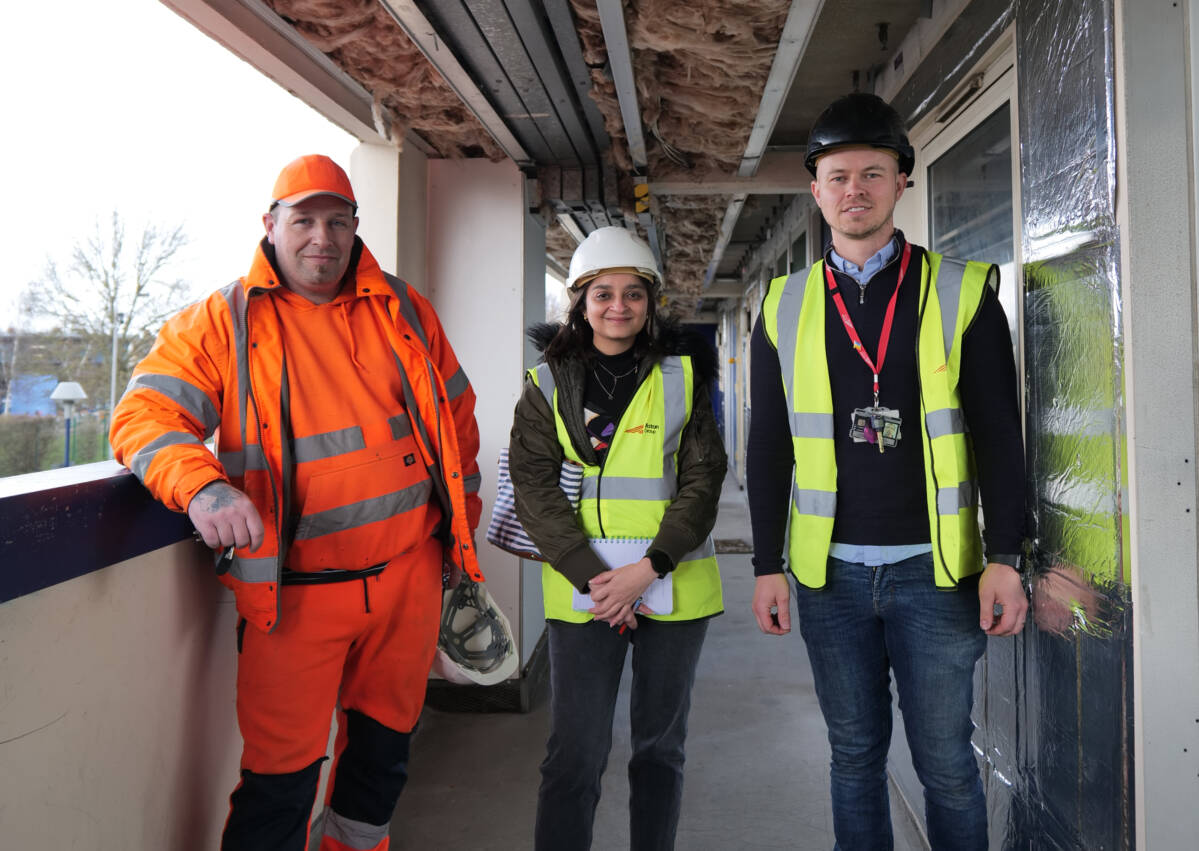
The Challenge
The existing materials that needed to be removed were in communal areas, including in stairways and balconies. This meant that work would be carried out right outside residents’ doorways. As a result, we would need to work in such a way that residents could still access and leave their homes. Access to garages would also need to be managed during the removal of materials. As such, clear lines of communication between our teams and the residents would be absolutely key.
As the work would also be carried out on the balconies, it was additionally necessary to find a way to protect anyone beneath the balconies from potential falling debris as we removed panels and fittings.
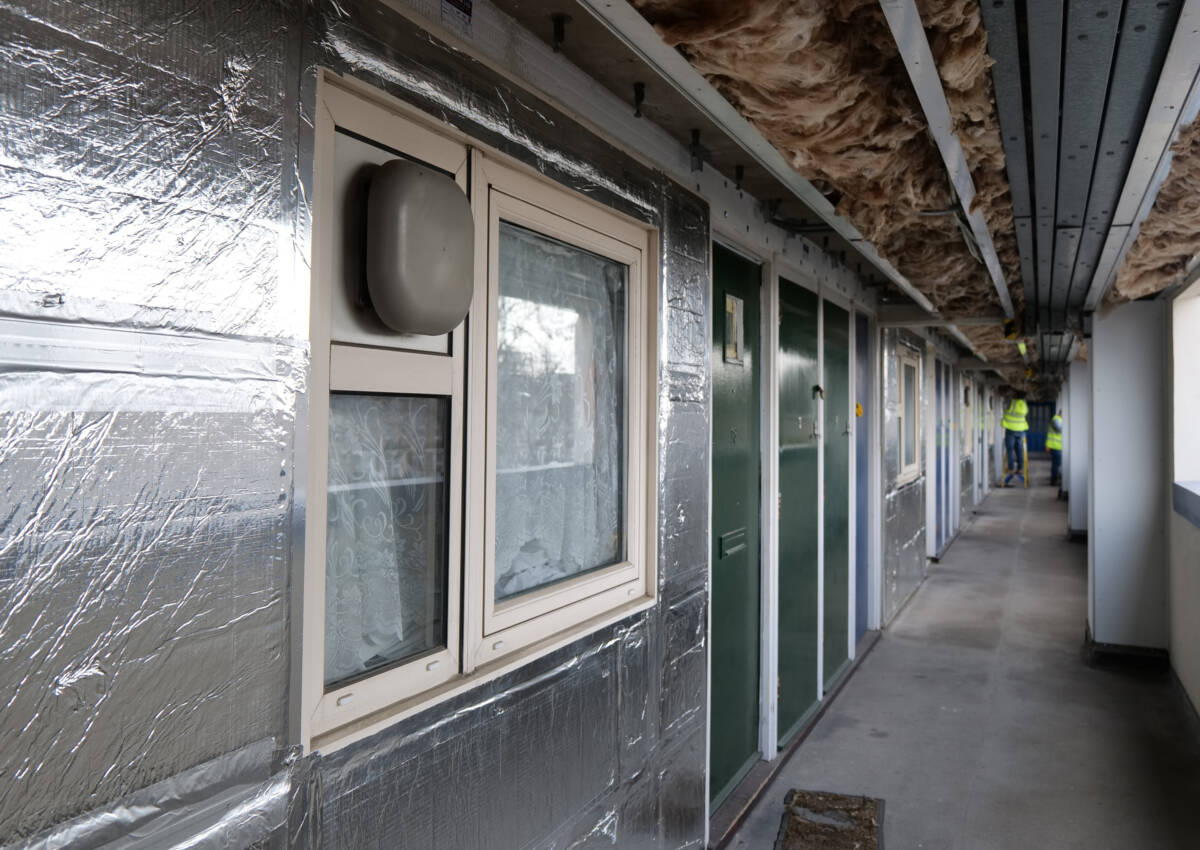
Walls being prepared
“Aston Group took full control and responsibility in a professional and very helpful manner – it is always a pleasure dealing with contractors who make projects easy. The project actually came in under budget and Astons actively looked at alternative approaches to reduce costs and time”
The Solution
To manage the design, installation and sign off of the works, we appointed Frankham Consultancy Group in the role of Principal Designer and Fire Engineer.
Before work began, we created a Resident Booklet, which explained what remedial works would be carried out and how. We also appointed a Resident Liaison Officer, who would be available throughout the works to handle any resident queries and deal with their concerns.
We then cleaned and laid down protective flooring in void flats to use for work cutting areas and respite for our team.
Protective screens were then mounted on the balconies to prevent debris from falling. Dust screens, complete with zip-up doors, were also set up in the corridors to protect residents while also allowing access when needed.
To maintain access to the garages during the works, we installed a movable tower in the car park. This meant that it could be shifted out of the way to provide vehicle access to residents and then moved back again to assist our teams.
To ensure that the materials in these residential blocks meet current fire safety regulations, T&S Environmental carefully began the process of removing HPL (high pressure laminate) panels and existing XPS (extruded polystyrene) insulation and associated fixings in the communal walkways, balconies and stairwell lobbies. Our experienced teams then fitted Euroclass A1 or A2 s-1 standard insulation as well as Hardie panelling.
This removal and replacement was then certified by an approved installer, who kept the buildings’ records up to date to ensure there was no break in the Golden Thread of information.
While carrying out our work, our team also checked roof compartments, which were repaired if necessary. Doors were fitted with new fire boarding surrounds and combustible material above the garage doors was also removed and replaced.
Once work was complete, we attached QR codes to the buildings. These codes lead to information on the fire safety work carried out, providing peace of mind to the residents and useful information to fire services.
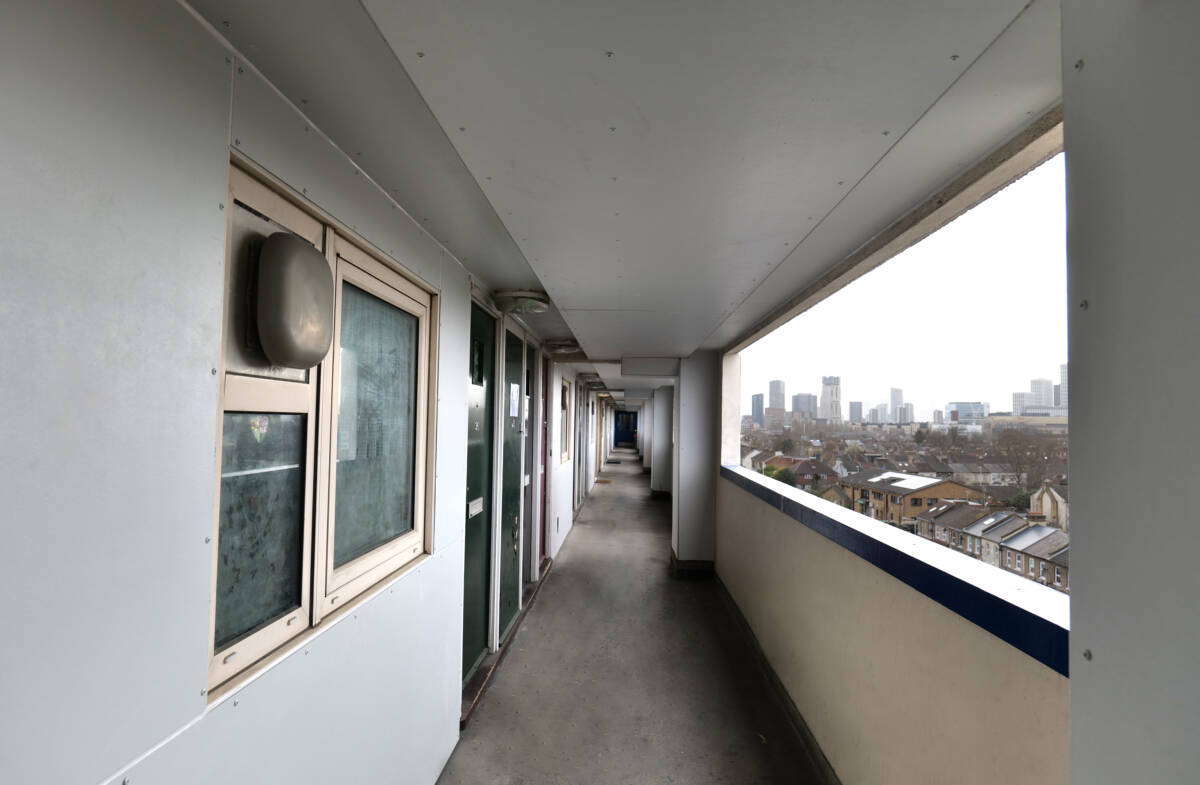
Completed corridor
The Results
As a result of our work, potentially combustible insulation and panelling has been removed from the Avenue Road residences. These materials have been replaced with those that meet the latest fire safety regulations. This has meant that the waking watch has ended.
Thanks to detailed recording throughout our work, which was certified by approved installers, the buildings’ records have also been updated. This ensures that a complete Golden Thread has been maintained, which can be relied upon by personnel responsible for the residences.