Lift Upgrade to High Rise Tower Block
Lift upgrades were required in two 1960s high-rise tower blocks requiring four lifts in total.
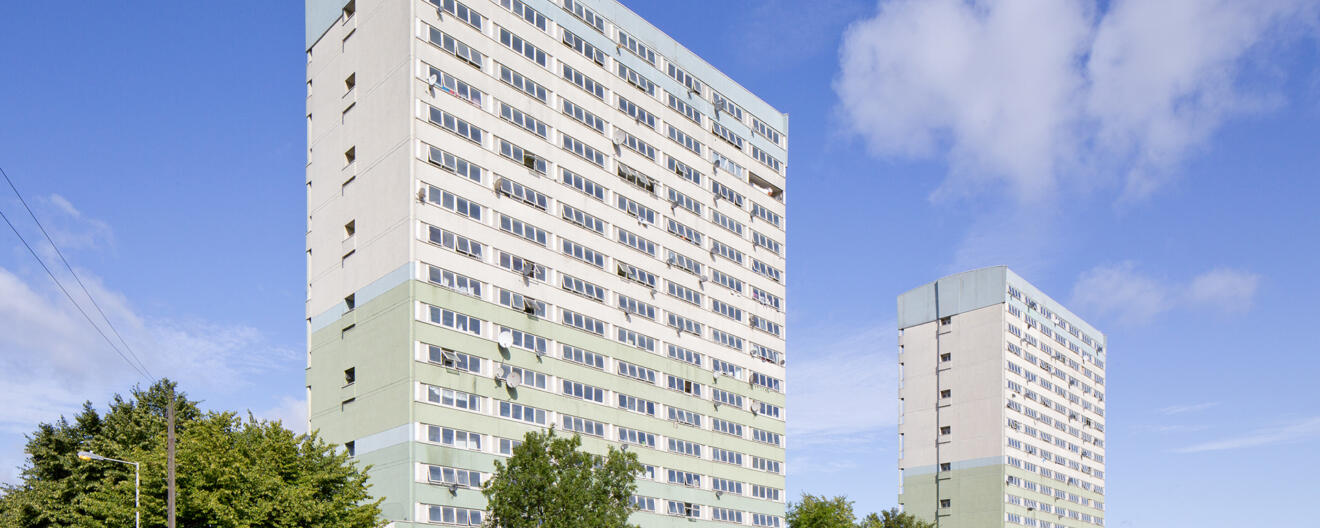
- Lift upgrades required in two 1960s high-rise tower blocks (two lifts per block)
- Complex post-Grenfell regulations and recommendations needed to be met
- Upgrades carried out while one of the lifts remains operational to minimise disruption
- Works part of a wider major refurbishment programme whilst in occupation
- Weekly inspection and service regime for single operational lift in each block whilst refurbishment in progress
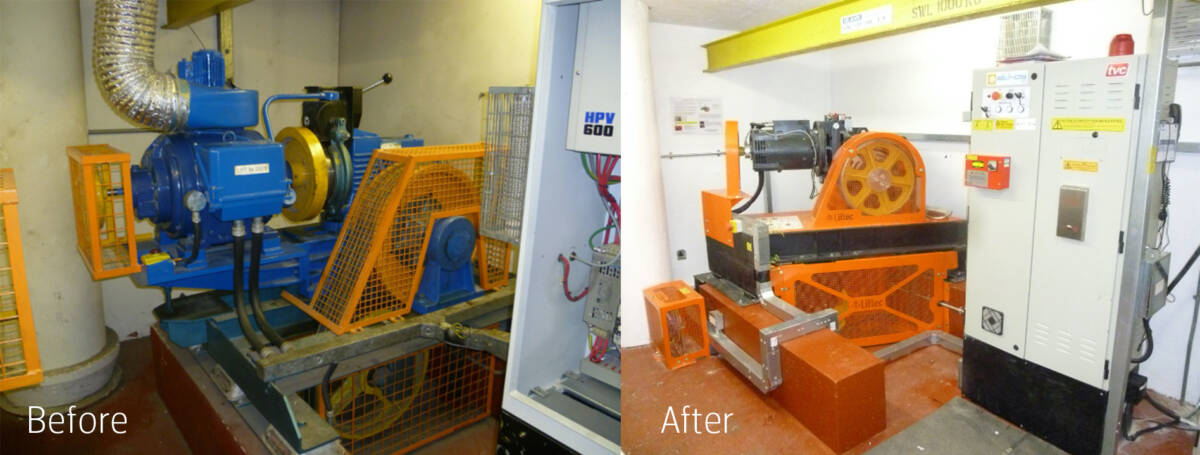
Before and after the installation
Fred Wigg and John Walsh Towers are two residential tower blocks in Leytonstone, within the London Borough of Waltham Forest, which were erected in the 1960s. Each tower is built over 17 floors, and houses 116 flats. Waltham Forest Council took the decision several years ago to upgrade all four lifts (two in each tower).
Aston Group has been working with Butler & Young Lift Consultants Limited (BYLCL) for almost 10 years, supporting them in the provision of their partnership with Waltham Forest Council to provide domestic lift management and replacement services.
Following the completion of a partial modernisation in 2018 to extend the life of the existing 10-person lifts, BYLCL was commissioned, in the wake of the Grenfell Tower tragedy, to carry out a feasibility study to determine what options were available for the lifts to comply with the current standards for firefighter lifts. These standards ensure that, in the event of a fire, the fire brigade can use the lifts to access all floors and evacuate tenants quickly and safely.
As part of the study, the load and speed of the lifts were considered. Only a minimal increase in speed was possible, but the load and car size could be increased to 1,000kg (13 persons). Structural surveys were required to ensure that the building could take the increase in load and that the entrances were high enough to allow for the raised landing thresholds.
The new larger lift car could accommodate the necessary rescue traps and ladders for firefighters. New fire-certified lift landing entrances could also be installed, with raised thresholds to minimise the ingress of water to the lift shaft.
Following the feasibility study, the decision was taken to go ahead and install firefighting lifts. This significantly changed the specifications of the project due to the number of regulations that now needed to be met.
To carry out this type of extensive modernisation in an occupied building, while maintaining a functioning lift within the same lift shaft, is extremely challenging from an operational, design and installation perspective. The programme of work was based on an agreed installation process, working from a modified platform to allow the new guide rails to be installed while still running on the old ones. This reduced the time and cost considerably, as the traditional method would have required the installation of a full-height scaffold in the lift shaft.
We used the same standardised lift equipment installed across the borough, ensuring that any engineer would be familiar with the system, thus reducing downtime. Aston Group agreed with residents that we would only undertake noisy drilling work between 10am-3pm on weekdays, as opposed to the normal legal hours of 8am-5pm.
Tenants will benefit from a faster, smoother ride, a brighter car with LED lighting, and the latest two-way emergency communication system. The new motor runs at a cooler temperature and is more efficient than the previous motor. New lift guides have been installed as well as new ropes, doors, tracks, matrix, car panel and CCTV camera.
Because the lift is a firefighting lift, a separate power supply has been installed. The power source comes from an on-site generator, which ensures the lift can switch from the normal power source to the generator seamlessly and with no downtime.
Works delivered by our supply chain partner Liftec Limited