Boosted Cold Water Services
Replacing the cold water services in an occupied 25-storey high rise
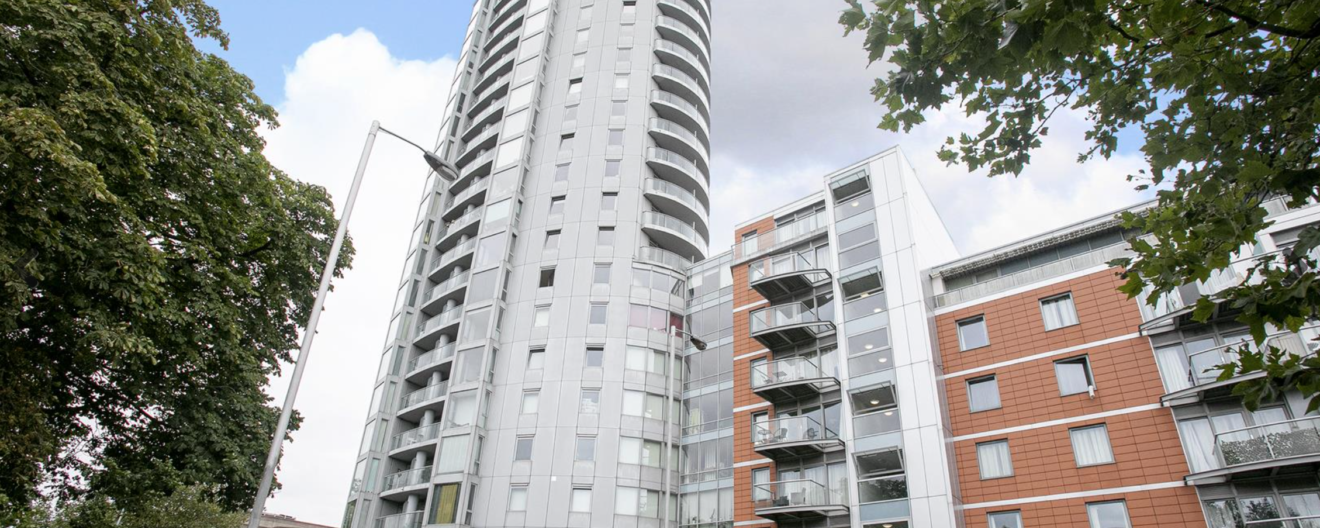
- New water main installed in the fire escape stairwell, from the ground floor to the 25th storey
- Leak detection system installed
- Alarm system fitted for faults in the water line
- Associated electrical and building works carried out
As Croydon’s fourth tallest building, Altitude 25 is an imposing structure reaching up 25 storeys. It was completed in 2009, but since then a series of leaks from its cold water main have caused thousands of pounds worth of damage.
At times, this damage has been so severe that residents have had to vacate their residence while repairs to their properties were completed. They have also gone without water for a number of days at a time while pipework was repaired.
Because of this ongoing issue, Aston Group were called in to replace the boosted cold water main and put a stop to the cycle of leaks.
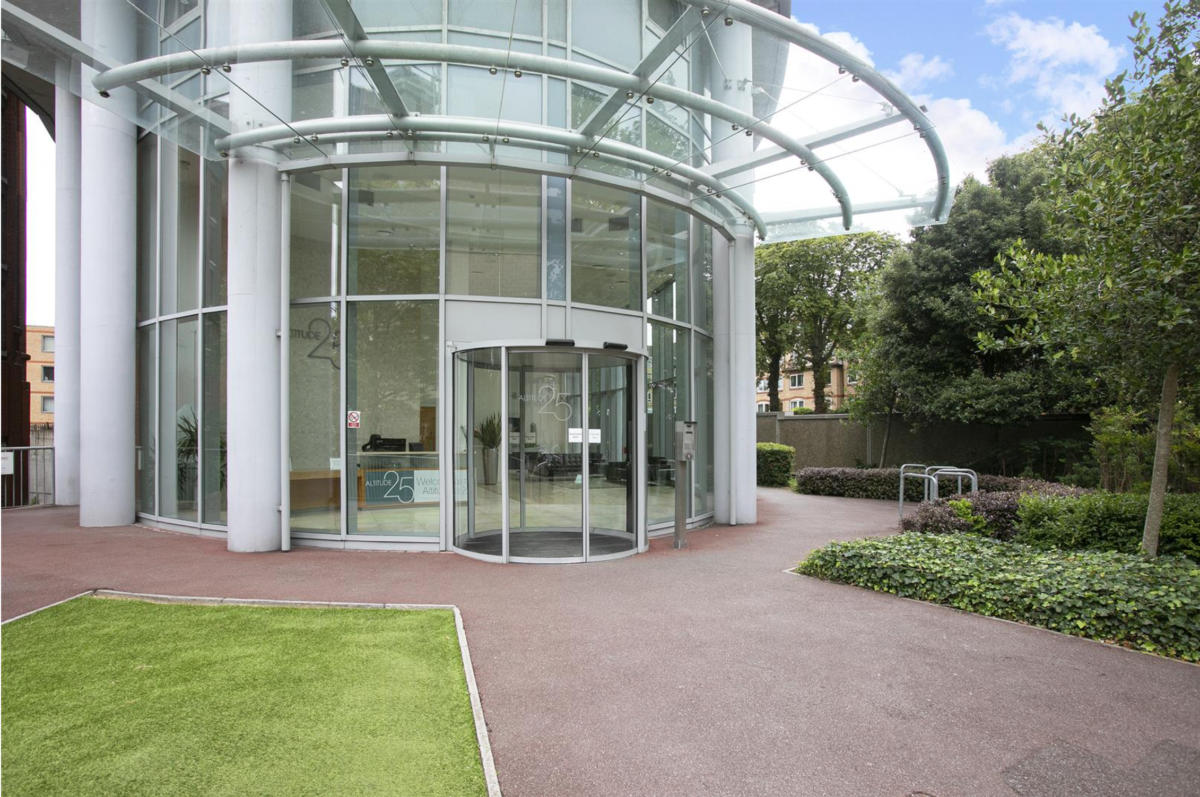
The Challenge
The new cold water service was needed urgently but it was imperative that the works were completed while the building was occupied, with minimal interruption to the occupants.
This presented a significant difficulty as the new water main was to be run through the fire escape stairwell, from the ground floor all the way up to the 25th level. Branches of the system would then need to run through each floor’s lobby before entering the existing riser cupboards.
To limit disruption, residents would need to be informed about which area we were working in. Access would also need to be possible for residents in those areas of work when required.
In terms of the work itself, the challenge was also significant. We had to set out core drilling, creating 120mm to 200mm holes through to each level inside the stairwell, and install 32mm to 110mm pipework throughout the building. All associated electrical and building works in the lobby areas needed completing too.
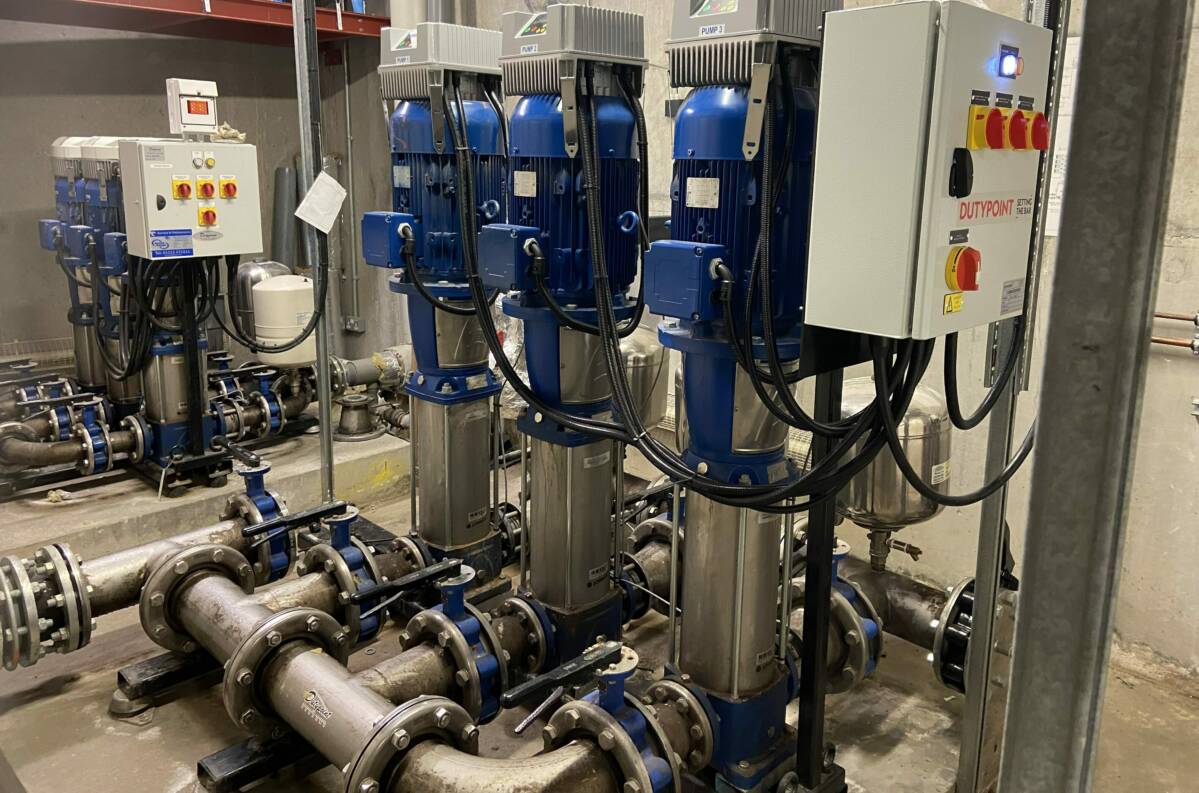
The Solution
To prevent lengthy periods of no water service for residents, we decided to keep the existing cold main in service while the new pipework was installed.
Work then began with core drilling in the stairwell, which we ensured was only carried out at agreed times to limit noise disturbance. We also implemented systems for the extraction of dust and safety protocols for the possibility of drilled concrete falling during drilling. Each time drilling was started, we closed sections of the stairwell, which were then monitored in case residents needed to use the stairs. Every day, notices were placed in the lifts and stairwell entrances to advise residents and visitors about which areas were being worked on.
For the pipework installation, all material was either brought to site on the day or stored in a designated basement area. At no time was material stored in the lobbies or stairwell, which would have restricted residents’ movement around the building.
Once the main riser in the stairwell was completed, we started on each branch through the lobbies. Suspended ceiling tiles had to be removed so that we could conceal some of the pipework for an improved aesthetic.
Pressure testing of the new pipework was then carried out while residents continued to use the existing water supply.
A shutdown of services then became unavoidable so that we could replace the pump inverters. However, we completed the connection of the new pipework to the pump-set and inverter replacement in just four hours.

At this point the building had another large leak from the existing water main, which resulted in the top half of the building having no water supply. Because of this, we scheduled additional resources to work through the weekend to make final connections from the new pipework to the supplies in the riser cupboards. This meant that we were able to move all of the residents over to the new water main quickly, which reduced the need for further repair work on the existing main as well as reducing residents’ time without cold water.
As a final part of the project, we installed a leak detection system that would shut down the booster pumps should a leak be detected. This was created by installing a main water meter in the plant room, which records water usage against all the secondary meters in the riser cupboards on each floor’s lobby. Should the water usage record higher figures from the main meter compared to the combined secondary metres, we know there is a leak. An alarm will then trigger a beacon in the ground floor lobby and flag up the issue on the building manager’s computer. The system will also raise an alarm for the building manager should excessive water be used on a single floor, as this may also indicate a fault in the water line.
The Results
The residents in Altitude 25 now have a reliable source of water that will not be shut down due to multiple leaks, cause costly repairs due to water damage or force them to vacate their homes.
With the leak detection system in place, the residents will also not need to continue their routine walks of the building to check for leaks.
Finally, water supply pressure and flow rate are now steady with no fluctuations throughout the day due to demand in peak periods.