Boiler Plant Replacement
Replacing the boilers and associated equipment in the plant room
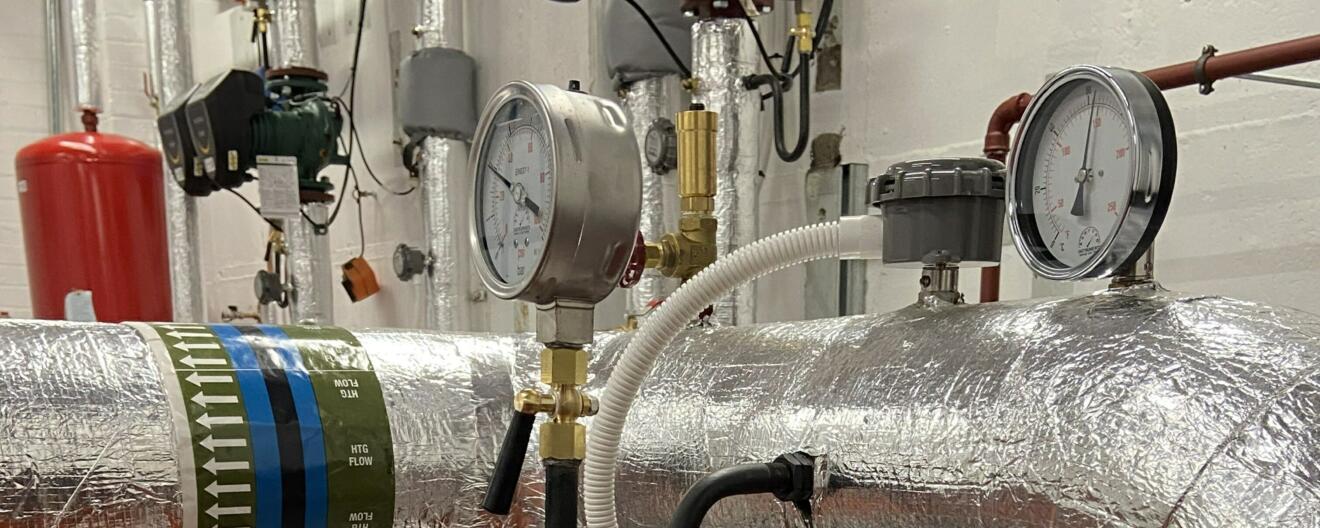
- Creation of a controlled environment for asbestos removal
- Installation of a new pipework and boilers in the plant room
- Fitting of a plate heat exchanger
- Implementation of a Magnaclean system filter
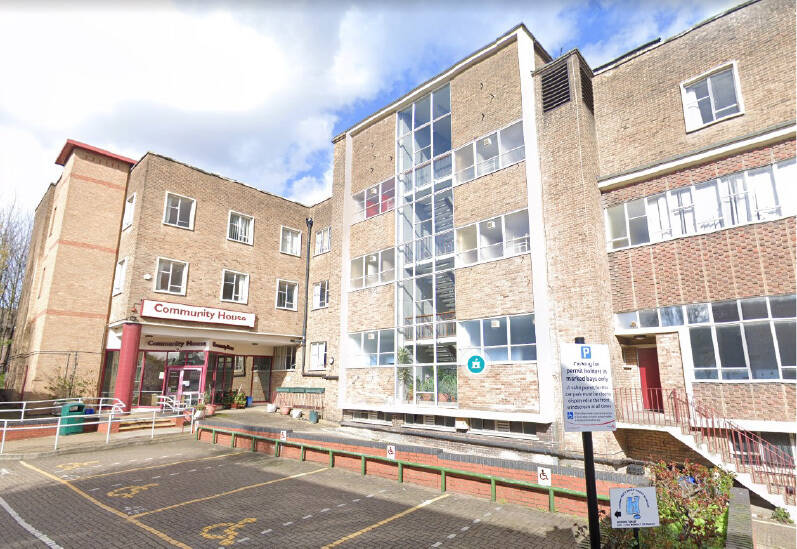
Community House is a multi-tenanted building that provides meeting spaces and office facilities to a large number of community groups and associations.
Unfortunately, the existing boilers recently failed beyond repair and needed to be replaced. With winter on the horizon, it was imperative that this replacement was made before the cold set in.
Aston Group was therefore called in to replace the boilers and associated equipment in the plant room. By doing so, we could help Community House’s multiple groups to continue serving their local communities throughout winter.
The Challenge
Before the project could start, we discovered that the plant room would need to be stripped of asbestos-contaminated material.
As a result, asbestos insulation residue had to be removed from all of the pipework within the plant room. The pipe penetrations would then have to be sealed and re-encapsulated within the walls of the plant room.
This created a delay for the replacement works. With the project under tight time constraints, we had to be as productive as possible to ensure the heating would be live in the first week of October.
The Solution
To support the asbestos removal, our team had to completely seal-off the working environment under fully controlled conditions. This included putting air monitoring in place so that no asbestos residue or fibre could escape during the removal process.
To ensure no time was wasted, all the new pipework was measured up before the asbestos removal took place. This was then prefabricated off-site while the strip-out commenced. As soon as the plant room was clear, all the new pipework was brought to site and bolted together
We then installed additional connections to facilitate a temporary boiler should the project overrun into the colder months. Fortunately, we managed to get all the installations in place in time, which meant that the temporary boiler was not required.
Due to the fact that the old boilers had been damaged by poor water quality, we completely flushed the system during installation. We then used a plate heat exchanger to separate the boiler water and system water to ensure that the latter would not affect the primary boiler water should it deteriorate over time. For added protection, we also fitted a Magnaclean system filter on the secondary circuit. This filtration system collects rust and other debris from the boiler and pipework to maintain efficiency.
As with most industries, manufacturing shortages caused delays. In this case, it led to the Building Management System (BMS) material being late to site. Due to this, we fitted temporary controls so that the building occupants could use the new plant in the interim.
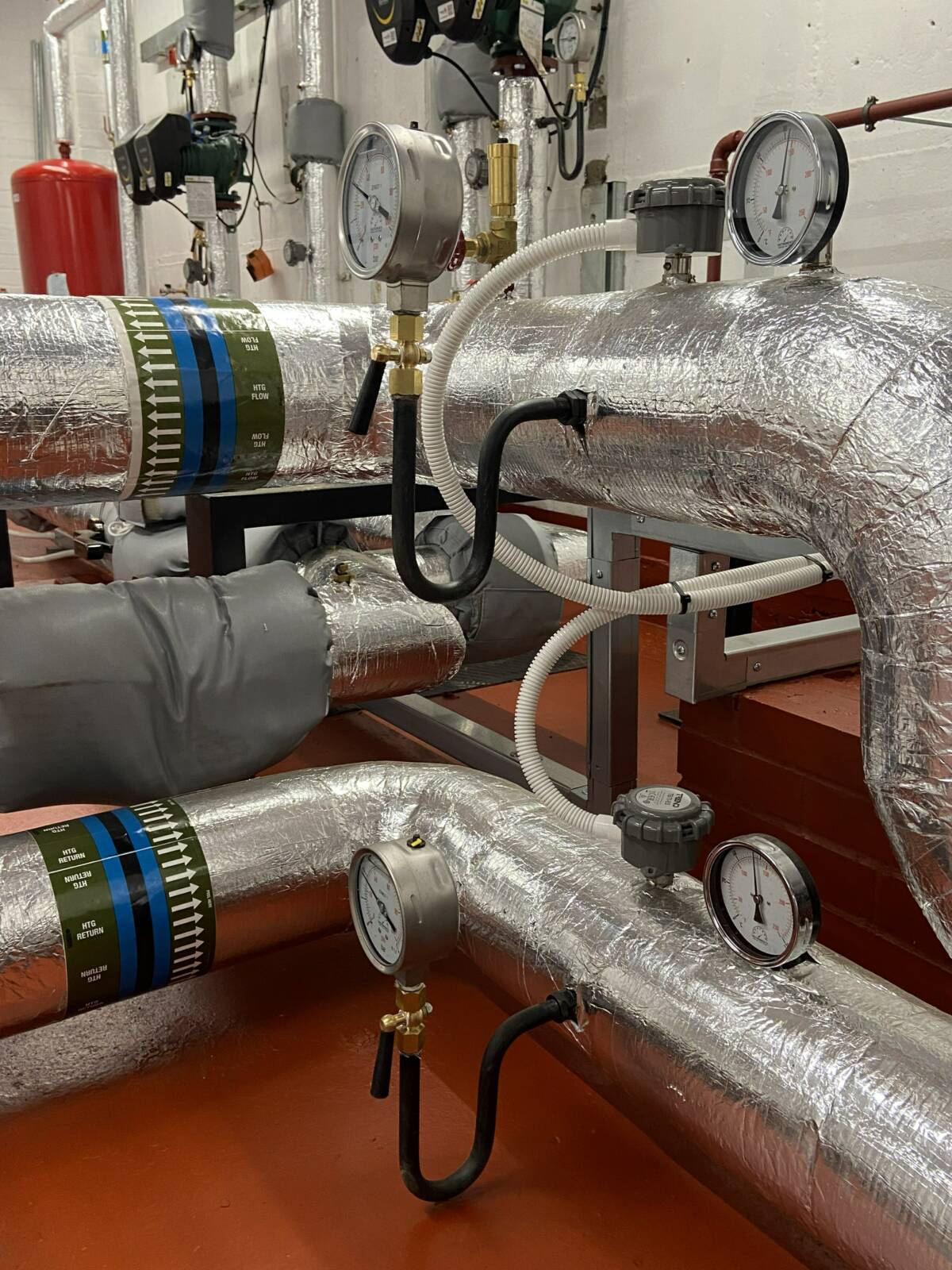
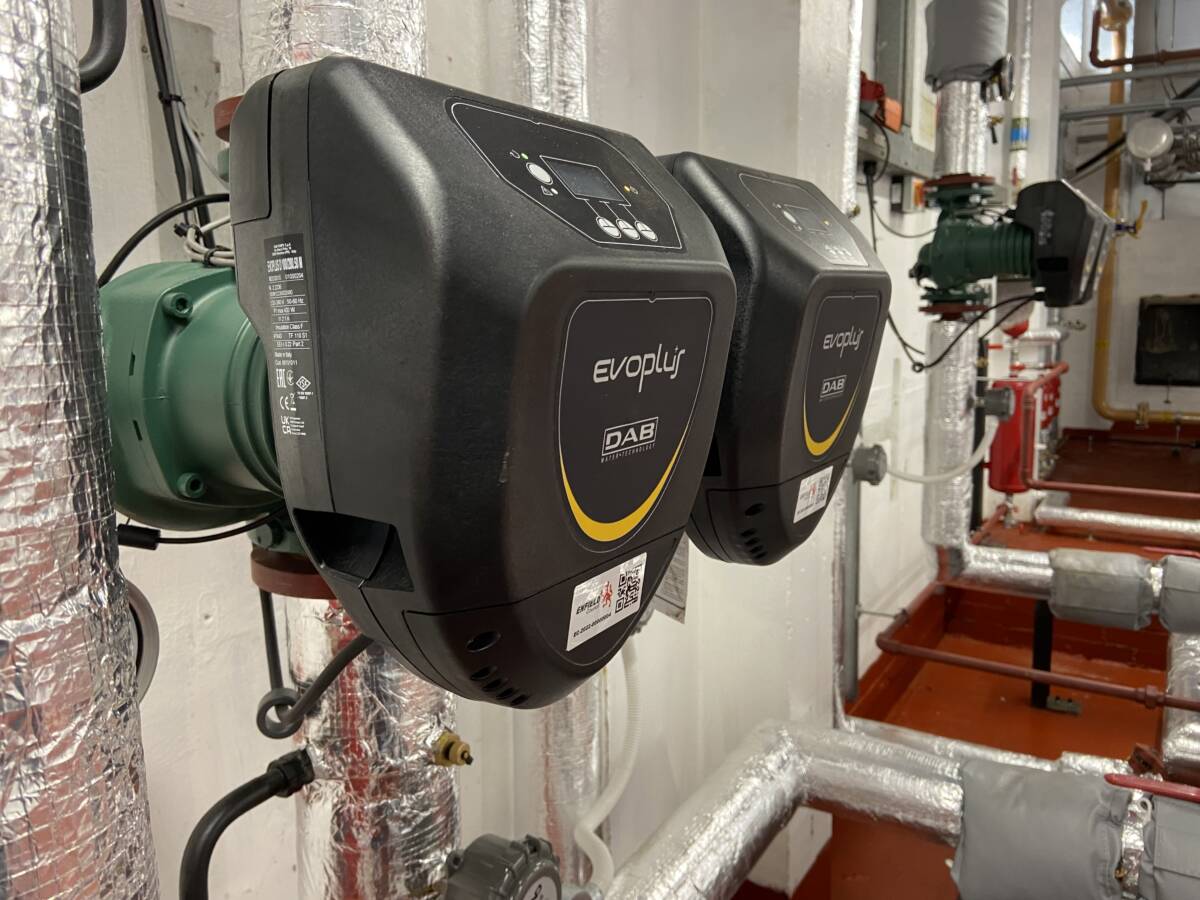
The Results
All asbestos was successfully and safely removed and the new pipework and boilers fitted. The new system became operational in the first week of October, meaning Community House was prepared for the cold months.
Thanks to this installation, the building’s occupants no longer have to worry about the reliability of the heating system and can continue to work in a warm environment throughout the winter.
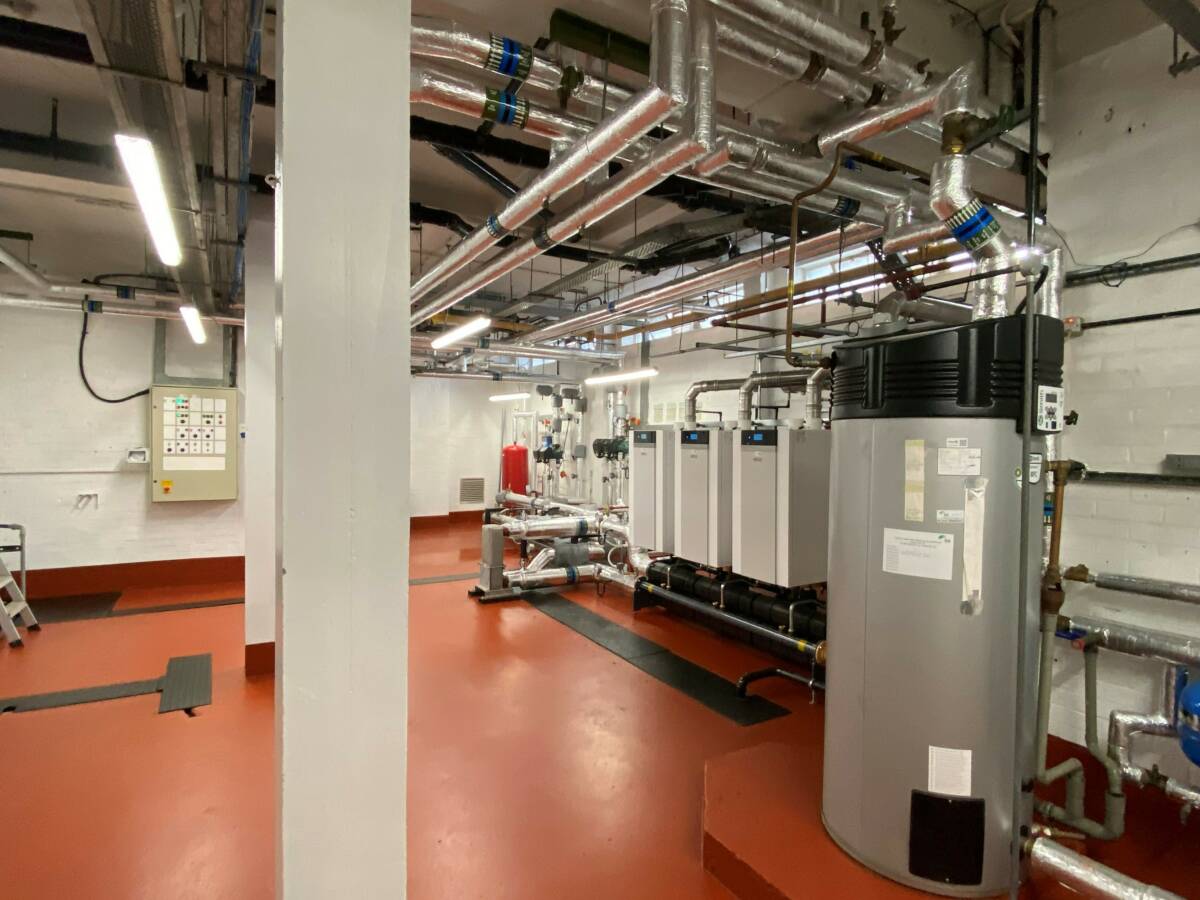